How are blankets made? This question unveils a fascinating journey from raw materials to the cozy comfort we experience under our blankets. The process involves a complex interplay of fiber selection, yarn creation, weaving or knitting techniques, finishing treatments, and design considerations. Understanding this process reveals the craftsmanship and technology behind these everyday essentials, highlighting the diverse materials and manufacturing methods that contribute to their warmth, texture, and durability.
From the sourcing of natural fibers like cotton and wool, or the creation of synthetic alternatives, to the intricate weaving or knitting processes that transform yarn into fabric, each step contributes to the final product. We’ll explore the various stages of blanket production, examining the differences between woven and knitted blankets, the impact of finishing processes on their properties, and the innovative technologies shaping modern manufacturing.
Raw Materials
Blanket manufacturing relies on a diverse range of raw materials, each contributing unique properties to the final product. The choice of fiber significantly impacts the blanket’s warmth, softness, durability, and cost, as well as its environmental footprint. Understanding these materials is crucial to appreciating the complexities of blanket production.
Fiber Types and Properties
Various fibers are employed in blanket production, each possessing distinct characteristics. Cotton, wool, and numerous synthetic fibers are commonly used, each offering a balance of properties that suit different needs and preferences. Cotton, a natural fiber, is known for its softness, breathability, and absorbency, making it suitable for warmer climates. Wool, another natural fiber, excels in warmth retention due to its unique crimp structure and natural insulation properties.
Synthetic fibers, such as polyester, acrylic, and microfiber, offer a range of characteristics including durability, wrinkle resistance, and affordability. These are often blended with natural fibers to enhance specific properties or reduce costs.
Sourcing and Processing of Raw Materials
The journey from raw material to finished blanket involves extensive processing. Cotton begins as cotton bolls, harvested and then processed through ginning to separate the fibers from the seeds. These fibers are then cleaned, combed, and spun into yarn. Wool, sourced from sheep, undergoes shearing, cleaning, and carding before spinning. Synthetic fibers are produced through chemical processes, involving polymerization and extrusion to create long continuous filaments.
These filaments are then cut, crimped, or otherwise treated to achieve the desired texture and properties before spinning into yarn.
Environmental Impact of Raw Materials
The environmental impact of blanket production varies considerably depending on the chosen fiber. Cotton cultivation can be resource-intensive, requiring significant amounts of water and pesticides. Wool production, while often associated with grazing animals, can contribute to land degradation and greenhouse gas emissions. Synthetic fibers, derived from petroleum, contribute to plastic pollution and have a significant carbon footprint.
However, advancements in sustainable farming practices for cotton and wool, alongside the development of recycled and bio-based synthetic fibers, are mitigating some of these concerns. The selection of raw materials therefore necessitates a careful consideration of environmental sustainability.
Comparison of Blanket Fiber Properties
Fiber Type | Softness | Warmth | Durability | Cost |
---|---|---|---|---|
Cotton | High | Moderate | Moderate | Moderate |
Wool | High | High | High | High |
Polyester | Moderate | Moderate | High | Low |
Acrylic | Moderate | Moderate | Moderate | Low |
Microfiber | High | Moderate | Moderate | Low to Moderate |
Yarn Production
Yarn production is a crucial step in blanket manufacturing, transforming raw fibers into the continuous strands used for weaving or knitting. The process significantly impacts the final blanket’s texture, strength, and drape. Different spinning methods and fiber types lead to a wide variety of yarn characteristics, each suitable for specific blanket applications.
Spinning Processes
The spinning process involves aligning and twisting fibers to create a continuous yarn. Several methods exist, each offering unique properties. The most common methods are ring spinning, rotor spinning, and air-jet spinning. Ring spinning, a traditional method, produces strong, even yarns with a smooth surface. Rotor spinning, a faster and more economical method, creates softer, bulkier yarns, often used in blankets emphasizing warmth and comfort.
Air-jet spinning utilizes high-pressure air jets to twist fibers, resulting in fine, strong yarns suitable for high-quality blankets. The choice of spinning method directly influences the final yarn’s properties, impacting the blanket’s overall quality.
Yarn Types Used in Blanket Making
Various yarn types are employed in blanket production, each possessing distinct characteristics. Woolen yarns, made from wool fibers, offer excellent warmth and insulation. Cotton yarns provide softness, breathability, and absorbency, making them suitable for lighter blankets. Acrylic yarns are synthetic alternatives offering durability, affordability, and a wide range of colors. Blends combining different fibers, such as wool and acrylic, offer a balance of properties, for instance, the warmth of wool with the durability of acrylic.
The selection of yarn type depends on the desired blanket characteristics—warmth, softness, durability, and cost.
Fiber Strength and Texture Comparison
The strength and texture of yarns are heavily influenced by the fiber type used. Wool yarns are known for their inherent elasticity and softness, though their strength can vary depending on the breed of sheep and processing methods. Cotton yarns offer good strength and a relatively smooth texture, while linen yarns are strong and have a characteristic slightly rough texture.
Synthetic yarns, such as acrylic, nylon, and polyester, exhibit a range of strengths and textures, often tailored to specific applications. For example, acrylic yarns can mimic the softness of wool while maintaining greater durability. The choice of fiber impacts the overall feel and longevity of the blanket.
Yarn Production Flowchart
The steps involved in yarn production can be visualized as follows:Raw Fiber (e.g., cotton, wool, synthetic fibers) –> Cleaning and Opening (removing impurities and separating fibers) –> Carding (aligning and disentangling fibers) –> Combing (optional, for finer yarns) –> Drawing (attenuating and further aligning fibers) –> Spinning (twisting fibers into yarn) –> Winding (winding yarn onto bobbins or cones) –> Finishing (treatments such as dyeing, sizing) –> Finished Yarn
Weaving and Knitting
Blankets are created using two primary methods: weaving and knitting. Both techniques interlock yarns to create fabric, but they differ significantly in their structure, resulting in blankets with varying properties. Understanding these differences helps consumers choose blankets appropriate for their needs.
Woven Blankets
Woven blankets are constructed by interlacing two sets of yarns at right angles—the warp (lengthwise) and the weft (crosswise). This creates a strong, durable fabric with a relatively stable structure. The process involves a loom, a machine that holds the warp yarns taut while the weft yarns are interwoven. Different types of looms exist, ranging from simple hand looms to complex, automated industrial looms.
The simplest hand looms use heddles to raise and lower warp threads, allowing the weft to pass underneath. More complex looms use a shuttle to carry the weft yarn across the warp. The resulting fabric is characterized by its strength and evenness, although the drape can be less flexible than knitted fabrics. Examples of woven blankets include traditional wool blankets, often characterized by their tightly woven structure and durability, and cotton blankets, which tend to be softer and more breathable.
Knitted Blankets, How are blankets made
Knitted blankets are created by interlocking loops of yarn, forming a series of interconnected nodes. This process uses needles, either manually (hand-knitting) or mechanically (machine-knitting). Knitting offers greater flexibility in terms of stitch patterns and textures. Different knitting techniques, such as stockinette stitch (alternating rows of knit and purl stitches), garter stitch (all knit stitches), and cable knitting (creating textured patterns by twisting stitches), produce varied surface textures and drape.
The flexibility of knitting allows for creating blankets with intricate designs and patterns, unlike woven blankets where intricate designs are usually achieved through the yarn itself rather than the weaving process. Examples include chunky knit blankets, known for their thick, cozy texture, and finer gauge blankets with intricate patterns.
Comparison of Woven and Knitted Blankets
The following table summarizes the key differences in warmth, drape, and durability between woven and knitted blankets:
Property | Woven Blanket | Knitted Blanket |
---|---|---|
Warmth | Generally warmer due to tighter weave, trapping more air. The warmth can vary significantly depending on the fiber and weave density. | Warmth varies significantly depending on the yarn weight and stitch pattern. A tightly knitted blanket with a thick yarn can be very warm. |
Drape | Less drape, tends to be stiffer and less flexible. | More drape, generally softer and more flexible, often exhibiting a more flowing appearance. |
Durability | Generally more durable and resistant to wear and tear, especially with tighter weaves. | Durability varies with the yarn and stitch pattern. Loosely knit blankets may be less durable, while tightly knit blankets can be quite durable. |
Finishing Processes

Blanket finishing encompasses a series of crucial processes that transform woven or knitted fabric into the soft, durable, and aesthetically pleasing products we know and love. These processes significantly impact the final quality, feel, and longevity of the blanket, and often involve considerations of environmental sustainability. The specific steps employed vary depending on the blanket’s fiber content, intended use, and desired characteristics.
Finishing processes broadly include cleaning, modifying the fabric’s properties, and preparing it for packaging and sale. These steps are essential for ensuring the blanket meets quality standards and consumer expectations. Improper finishing can lead to shrinkage, uneven dyeing, or a rough texture, diminishing the product’s value.
Washing and Drying
Washing removes residual sizing, oils, and other impurities from the fabric left over from the manufacturing process. Different washing methods, including scouring and bleaching, are used depending on the fiber type and desired outcome. Scouring employs detergents to remove impurities, while bleaching uses chemicals to whiten the fabric. The subsequent drying process is carefully controlled to prevent shrinkage or damage to the fibers.
Modern techniques utilize controlled temperature and humidity to ensure consistent results. For example, a wool blanket requires a gentler drying process than a cotton blanket to avoid felting.
Shearing and Finishing Treatments
Shearing, particularly relevant for blankets with a napped surface like fleece, involves trimming the fibers to achieve a uniform height and texture. This process creates a softer, more even surface. Further finishing treatments are often applied to enhance the blanket’s properties. These treatments can include pre-shrinking to minimize shrinkage after washing, dyeing to add color and vibrancy, and applying flame retardants to enhance safety.
Pre-shrinking processes involve controlled washing and drying cycles to achieve dimensional stability. Dyeing techniques can range from simple immersion dyeing to more complex processes like reactive or disperse dyeing, selected based on the fiber type and desired colorfastness. Flame retardants, typically applied through a chemical treatment, reduce the blanket’s flammability.
Blanket manufacturing involves various processes, from fiber sourcing to weaving and finishing. The energy required for these processes, particularly in synthetic blanket production, often relies on fossil fuels; understanding the energy equivalence is crucial. For instance, to grasp the scale of energy consumption, consider that the heat generated from burning a ton of coal is roughly equivalent to the energy from a significant amount of wood, as detailed in this informative article: 1 ton of coal equals how much wood.
This energy comparison helps illustrate the environmental impact associated with different blanket manufacturing methods and material choices.
Environmental Concerns and Sustainable Alternatives
Many traditional finishing processes utilize significant amounts of water and energy, and generate wastewater containing dyes and chemicals. These can have negative environmental impacts. For instance, some dyes can be toxic to aquatic life. Sustainable alternatives focus on reducing water and energy consumption, using less harmful chemicals, and employing closed-loop systems to recycle wastewater. Examples include using low-impact dyes, adopting water-saving washing and drying technologies, and implementing responsible waste management practices.
The development and adoption of biodegradable and recyclable materials are also crucial aspects of sustainable blanket production.
Innovative Finishing Techniques
Recent advancements in finishing technologies have led to innovative techniques that enhance blanket properties. For example, treatments can be applied to improve water resistance, making the blanket suitable for outdoor use. Other treatments enhance softness by modifying the fiber’s surface, providing a more luxurious feel. These innovative techniques often leverage nanotechnology or advanced chemical processes to achieve specific functional properties without compromising the blanket’s comfort or aesthetics.
For example, a water-repellent finish could be achieved through the application of a durable water repellent (DWR) coating, making the blanket suitable for use in damp conditions. Similarly, a softening treatment could involve the use of specific chemicals that enhance the fiber’s smoothness and flexibility.
Blanket Types and Designs: How Are Blankets Made
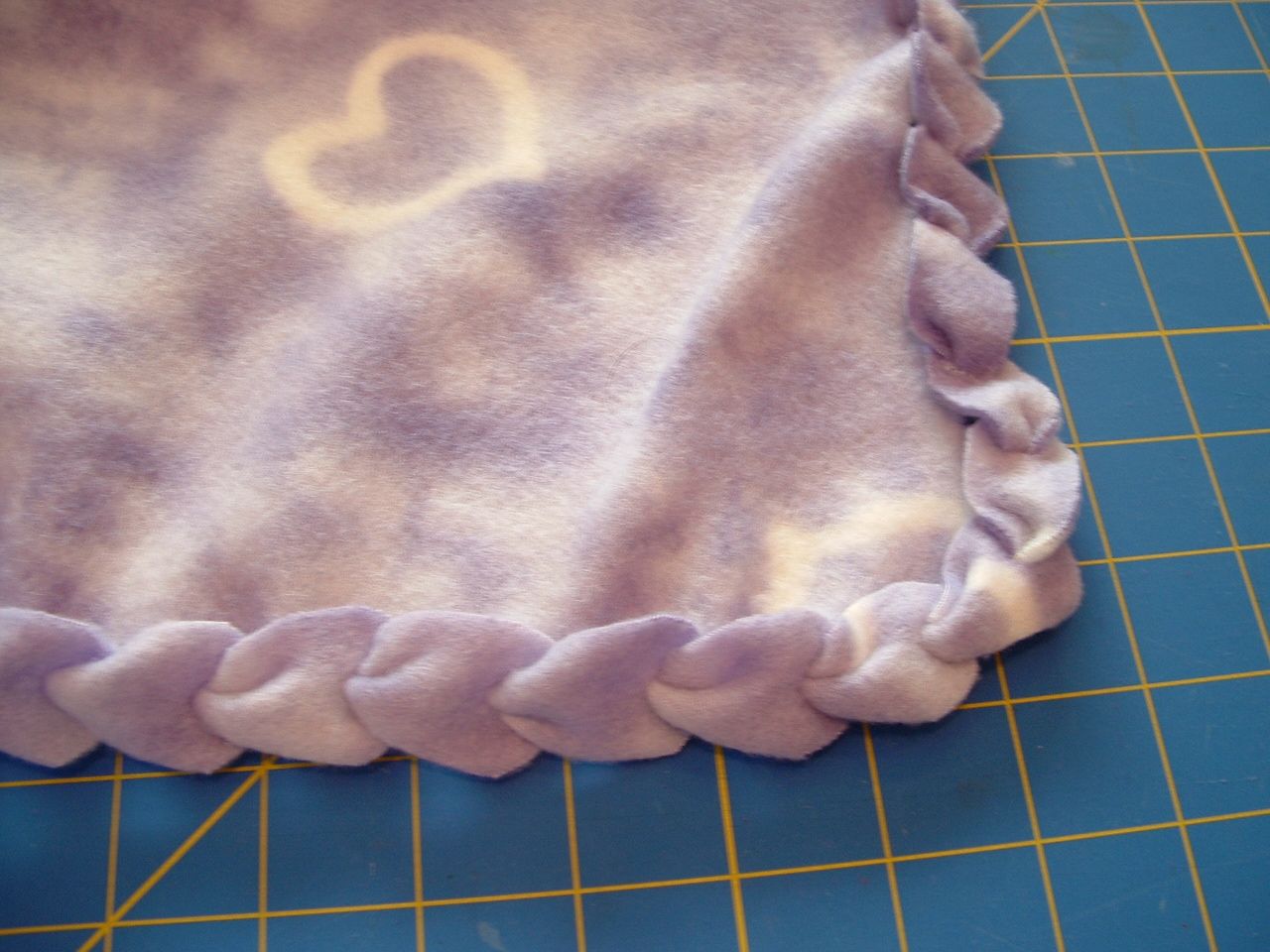
Blankets, seemingly simple items of comfort, encompass a vast array of types and designs, reflecting diverse materials, construction techniques, and cultural influences. Understanding these variations provides insight into the rich history and ongoing evolution of this essential textile.Blankets are categorized based on material, construction, and intended use, resulting in a wide spectrum of options to suit individual needs and preferences.
Design elements such as pattern, color, and texture play a significant role in both the aesthetic appeal and functional properties of the finished product.
Blanket Types and Their Characteristics
Different blanket types cater to specific needs and preferences. Throws, for instance, are lightweight and often decorative, ideal for draping over furniture or providing a light layer of warmth. Afghans, typically handmade, showcase intricate patterns and textures, often carrying sentimental value. Quilts, composed of layered fabric stitched together, offer exceptional warmth and durability. Electric blankets provide a regulated source of heat, useful in cold climates or for individuals with specific temperature sensitivities.
Each type possesses unique characteristics that dictate its functionality and appeal.
Design Aspects of Blankets
The design of a blanket significantly impacts its overall aesthetic and functionality. Pattern creation involves selecting and arranging motifs, creating visual interest and often reflecting cultural or personal expression. Color choices influence the mood and ambiance, with warm tones conveying coziness and cool tones suggesting serenity. Texture variations, achieved through different weaving techniques or material combinations, add depth and tactile appeal.
For example, a chunky knit blanket offers a different sensory experience than a smooth, tightly woven one.
Categorization of Blanket Types
The following categorization system organizes blankets based on material, construction, and intended use:
- Material: Wool, cotton, fleece, silk, synthetic fibers (polyester, acrylic)
- Construction: Woven, knitted, crocheted, quilted, tufted
- Intended Use: Bed blankets, throws, afghans, travel blankets, electric blankets, baby blankets
This system allows for a more comprehensive understanding of the diverse options available and helps consumers choose blankets that best meet their individual needs.
Creating a Unique Blanket Design
The process of designing a unique blanket begins with conceptualization, where the designer envisions the overall aesthetic, functionality, and intended use. This involves considering the target audience, desired materials, and the overall style. Next, pattern development involves sketching or digitally designing the pattern, selecting colors, and determining the texture. Sample creation allows for testing and refinement of the design before mass production or final creation.
Finally, the chosen construction method (weaving, knitting, quilting, etc.) is employed to create the finished product. The entire process requires creativity, technical skill, and attention to detail. For example, a designer might start with a specific color palette inspired by a landscape, then develop a geometric pattern to complement it, finally choosing a soft, luxurious wool to create a cozy and visually striking blanket.
Manufacturing Technologies
Modern blanket manufacturing relies heavily on sophisticated machinery to achieve high production volumes and consistent quality. The integration of automated systems has significantly transformed the industry, impacting efficiency and cost-effectiveness compared to traditional, labor-intensive methods. This section details the role of machinery in different stages of blanket production and contrasts traditional and modern approaches.
Machinery in Blanket Production
Various types of machinery are employed throughout the blanket manufacturing process. In yarn production, carding machines disentangle and align fibers, while spinning machines twist the fibers into yarn. High-speed ring spinning and air-jet spinning machines are commonly used for producing yarn suitable for blankets. For weaving, shuttle looms and rapier looms create woven blankets, with modern air-jet looms offering higher speeds and efficiency.
Knitting machines, including circular knitting machines and flat knitting machines, are used for producing knitted blankets, with computerized models allowing for intricate designs and patterns. In finishing, machines such as washing machines, dryers, and shearing machines are used to process the finished blankets, ensuring softness and evenness. Finally, cutting and sewing machines are employed for cutting and sewing blankets made from multiple pieces of fabric.
Comparison of Traditional and Modern Methods
Traditional blanket making often involved hand-spinning and hand-weaving, a slow and labor-intensive process. This resulted in lower production volumes and higher costs, limiting the availability and affordability of blankets. Modern, automated processes, however, employ sophisticated machinery to perform these tasks efficiently. For example, automated spinning machines can produce significantly more yarn than a hand-spinner, and high-speed looms can weave blankets much faster than traditional hand-looms.
This increased efficiency leads to higher production volumes and lower per-unit costs, making blankets more accessible to a wider range of consumers. The precision of automated machinery also ensures a more consistent product quality, minimizing variations in texture, weight, and dimensions.
Impact of Technological Advancements
Technological advancements have significantly improved the efficiency and cost-effectiveness of blanket manufacturing. Automated systems have replaced many manual tasks, reducing labor costs and increasing production speeds. The development of advanced materials and manufacturing processes has also led to the creation of higher-quality, more durable, and innovative blanket designs. Computer-aided design (CAD) and computer-aided manufacturing (CAM) systems allow for precise control over the manufacturing process, reducing waste and improving overall quality.
These advancements have resulted in a wider range of blanket styles, colors, and textures being available at competitive prices.
Visual Representation of a Modern Blanket Manufacturing Facility
Imagine a large, modern facility spanning several acres. The building is clean, well-lit, and organized into distinct sections. The yarn production area houses rows of automated spinning machines humming quietly, with robotic arms tending to the machines and transferring spools of yarn. Adjacent to this is the weaving or knitting section, filled with large, high-speed looms or knitting machines, their rhythmic movements a testament to efficient production.
A separate area is dedicated to finishing processes, containing large industrial washing machines, dryers, and shearing machines. Finally, a cutting and sewing section is where multiple layers of fabric are cut and stitched into finished blankets. Throughout the facility, automated guided vehicles (AGVs) transport materials and finished products, minimizing manual handling and ensuring a smooth workflow. The entire operation is monitored and controlled by a sophisticated computer system, optimizing production parameters and ensuring consistent quality.
Workers are present to oversee the machines, perform quality checks, and troubleshoot any issues, but the majority of the production process is automated.
Closing Notes
The creation of a blanket, from initial fiber selection to final finishing, is a multi-stage process showcasing a blend of traditional techniques and modern technology. Understanding the journey from raw material to finished product allows us to appreciate the craftsmanship involved and to make informed choices when selecting a blanket. Whether prioritizing sustainability, specific material properties, or unique design aesthetics, consumers can leverage this knowledge to find the perfect blanket to suit their needs and preferences.
The next time you snuggle under a warm blanket, consider the intricate journey it undertook to reach your comfort.